Unraveling About Aluminum Casting: From Essentials to Know-how
Unraveling About Aluminum Casting: From Essentials to Know-how
Blog Article
Explore the Globe of Aluminum Casting: Insider Tricks and Approaches
In the realm of manufacturing, aluminum casting stands as an essential process, vital for the development of a large selection of items. Behind the relatively simple strategy exist a plethora of detailed aspects, frequently unbeknownst to many. As we browse with the world of aluminum casting, there exists a realm of insider secrets and methods that can boost the high quality of the last products and streamline the production procedure. By revealing these hidden gems and exploring the subtleties of this craft, a whole brand-new dimension of opportunities arises, assuring to transform the means we perceive and engage with aluminum spreading.

The Basics of Aluminum Spreading
Light weight aluminum spreading, a basic process in manufacturing, includes the putting of liquified aluminum into a mold and mildew to attain wanted forms and structures. This flexible strategy is extensively used across different markets because of light weight aluminum's remarkable residential properties such as high strength-to-weight ratio, corrosion resistance, and thermal conductivity.
The process begins with the melting of light weight aluminum in a heating system at temperature levels exceeding 1220 ° F(660 ° C ) Once the aluminum reaches its liquid state, it is poured right into a pre-designed mold tooth cavity. The mold, generally made from products like steel or sand, determines the last shape of the actors light weight aluminum component.
After pouring, the aluminum is entrusted to cool and strengthen within the mold and mildew - about aluminum casting. This cooling duration is vital as it figures out the stability and quality of the final product. As soon as solidified, the mold and mildew is removed, disclosing the recently created light weight aluminum spreading
Expert Tips for Effective Casting
To accomplish optimal results in light weight aluminum spreading, careful interest to detail during the mold and mildew design stage is imperative for making certain effective results. Monitoring and managing the metal temperature level throughout the spreading procedure can help stop problems such as premature solidification or porosity in the last product.
Moreover, one more vital tip is to appropriately prepare the mold and mildew surface area. A well-prepared mold and mildew surface can contribute to much better steel circulation, minimized disturbance, and enhanced surface finish on the cast component. This preparation might entail utilizing therapies or layers to enhance mold and mildew release and avoid metal/mold interactions that might cause flaws. By paying close attention to these insider suggestions, manufacturers can improve the quality and performance of their light weight aluminum casting procedures.
Advanced Techniques in Light Weight Aluminum Casting
Making use of ingenious techniques and sophisticated techniques, the world of light weight aluminum spreading has seen a substantial advancement in the direction of progressed techniques that push the limits of standard methods. One such strategy is vacuum spreading, which involves producing a vacuum cleaner environment to get rid of air from the mold and mildew tooth cavity, resulting in greater quality and more complex spreadings with decreased porosity. In addition, financial investment spreading, also referred to as lost-wax spreading, is a refined technique that permits intricate shapes and slim walls, resulting in exact and thorough light weight aluminum components.
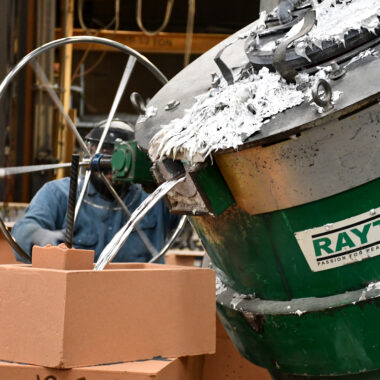
In addition, progressed simulation software application plays a critical duty in optimizing spreading designs and predicting possible defects, permitting adjustments to be made before the actual spreading process begins. By embracing these innovative methods, producers can elevate their light weight aluminum casting abilities to brand-new heights, satisfying the needs of modern industries with precision and development.
Comprehending Different Casting Techniques
Different casting approaches offer unique advantages and are picked based on factors such as the intricacy of the layout, production quantity, material demands, and price factors to consider. One of the most typical casting approaches is sand casting, where a mold and mildew is developed using sand as the main material.
An additional prominent spreading technique is die casting, which involves infusing liquified steel into a mold cavity under high pressure. By comprehending the subtleties of different spreading approaches, manufacturers can make enlightened decisions to maximize their production procedures and achieve the wanted end results.
Optimizing Performance in Casting Workflow
With a strong understanding of the nuances of various casting methods, makers can simplify their operations to boost efficiency in steel manufacture processes. Taking full advantage of effectiveness in casting operations needs a methodical approach that concentrates on optimizing every action of the casting procedure. One key approach is to execute lean production principles to remove waste and improve overall performance. By recognizing and getting rid of traffic jams in the production line, makers can improve operations and decrease lead times.
Furthermore, buying sophisticated innovation and equipment can dramatically boost efficiency in casting procedures. Automated systems, robotics, and computer-aided design (CAD) software application can streamline procedures, minimize mistakes, and boost outcome. Furthermore, training staff members on the most up to date methods and best methods can additionally add to optimizing efficiency in casting procedures.
Regular maintenance of equipment and devices is crucial to protect against breakdowns and decrease downtime - about aluminum casting. Applying an aggressive maintenance routine can help identify prospective issues prior to they intensify, guaranteeing smooth procedures and uninterrupted manufacturing. On the whole, by prioritizing performance and continual enhancement, manufacturers discover this can maximize their spreading procedures and stay competitive in the market
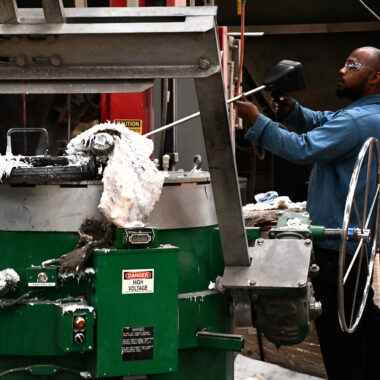
Conclusion
In conclusion, the world of aluminum casting uses a large array of chances for those looking to produce intricate and durable metal items. Understanding the different spreading techniques and optimizing performance in operations are crucial parts to attaining top quality outcomes in aluminum spreading.
One such technique is vacuum cleaner casting, which includes producing a vacuum setting to eliminate air from the mold and mildew tooth cavity, leading to higher quality and more detailed spreadings with reduced porosity (about aluminum casting). Furthermore, financial investment casting, likewise recognized as lost-wax casting, is a refined technique that enables for thin wall surfaces and complicated shapes, resulting in precise and detailed light this link weight aluminum components
One of the most usual spreading approaches is sand casting, where a mold Home Page and mildew is produced making use of sand as the main product.An additional prominent spreading approach is pass away casting, which includes injecting molten metal right into a mold dental caries under high pressure. Comprehending the various casting methods and maximizing performance in procedures are key elements to accomplishing high-quality outcomes in aluminum spreading.
Report this page